3D scanning - what is it?
What Is 3D Scanning?
3D scanning is a measurement technique that allows you to obtain a three-dimensional model of a physical object. This process is possible thanks to the use of 3D scanners, which measure the distance between the surface of the object and the measuring device, collecting hundreds or even thousands of points. These points are then processed to create a three-dimensional model that faithfully reproduces the shape and structure of the original. It is a process that has applications in various fields, from industry to medicine, opening the door to new possibilities for design, production and exploration. To understand the full scope of 3D scanning, it is worth looking at its basic aspects.
3D Scanning Methods
3D scanning, a key technology in the field of visualization and production, is constantly evolving, introducing new methods and techniques. Below is an overview of the most modern 3D scanning methods that shape the present and future of this fascinating field:
• Laser Scanning
One of the most widely used methods is laser scanning. It is a non-contact method of optically measuring three-dimensional objects using laser light. The technology works by measuring the distance and angle between the scanner and the surface of the object. This data is transformed into a point cloud, often consisting of millions or even billions of points. Thanks to its high precision, this method is used in design, reproduction of elements and quality control.
• Structured Light Scanning
Structured light scanning projects a light pattern (e.g. stripes or dots) onto the object. Cameras record the deformation of the pattern, allowing the software to recreate the 3D geometry. This method is particularly effective for small objects and measurements up to 3 meters. It can be used in both handheld and stationary scanners. It requires controlled lighting and a surface that properly diffuses light.
• Photogrammetry
Photogrammetry uses photographs taken from different angles to recreate a 3D model. A camera with known parameters captures multiple shots, which software analyzes to create a point cloud. This method is popular in surveying, mapping, film, gaming, and documenting large objects such as buildings or sculptures.
• Computed Tomography (CT)
Computed tomography (CT) makes it possible to create a 3D model of an object's interior by analyzing X-ray images taken at different angles. Industrial CT scanners allow not only for geometric measurements but also structural analysis, quality control, and detection of internal defects. This technology is used in medicine, industry, and metrology.
3D Scanning Process – Step by Step
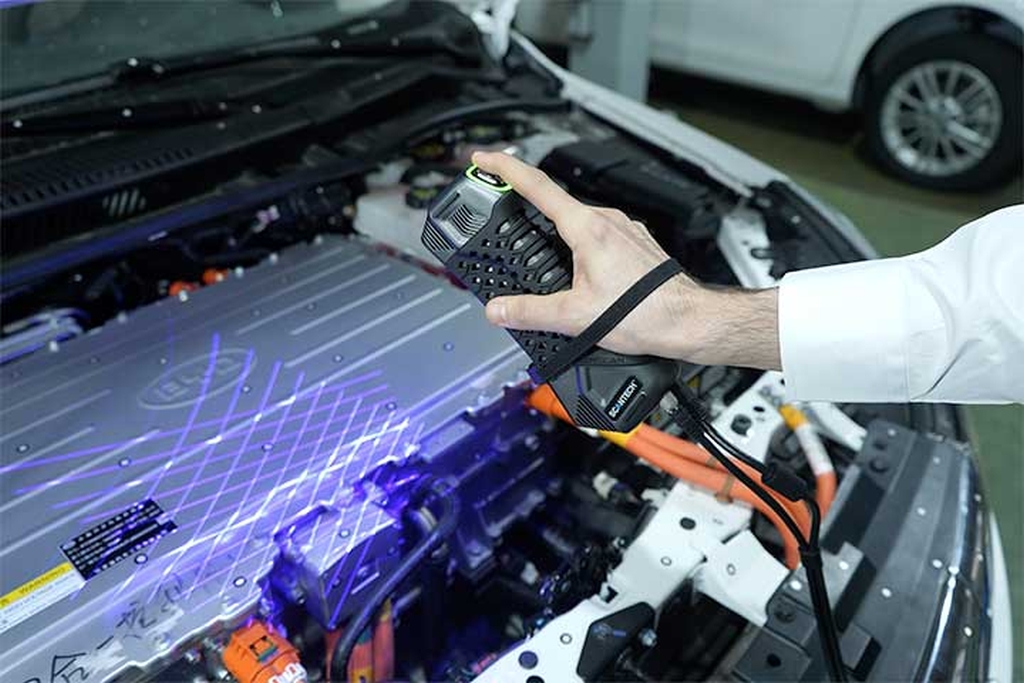
Below is a general step-by-step guide to the 3D scanning process:
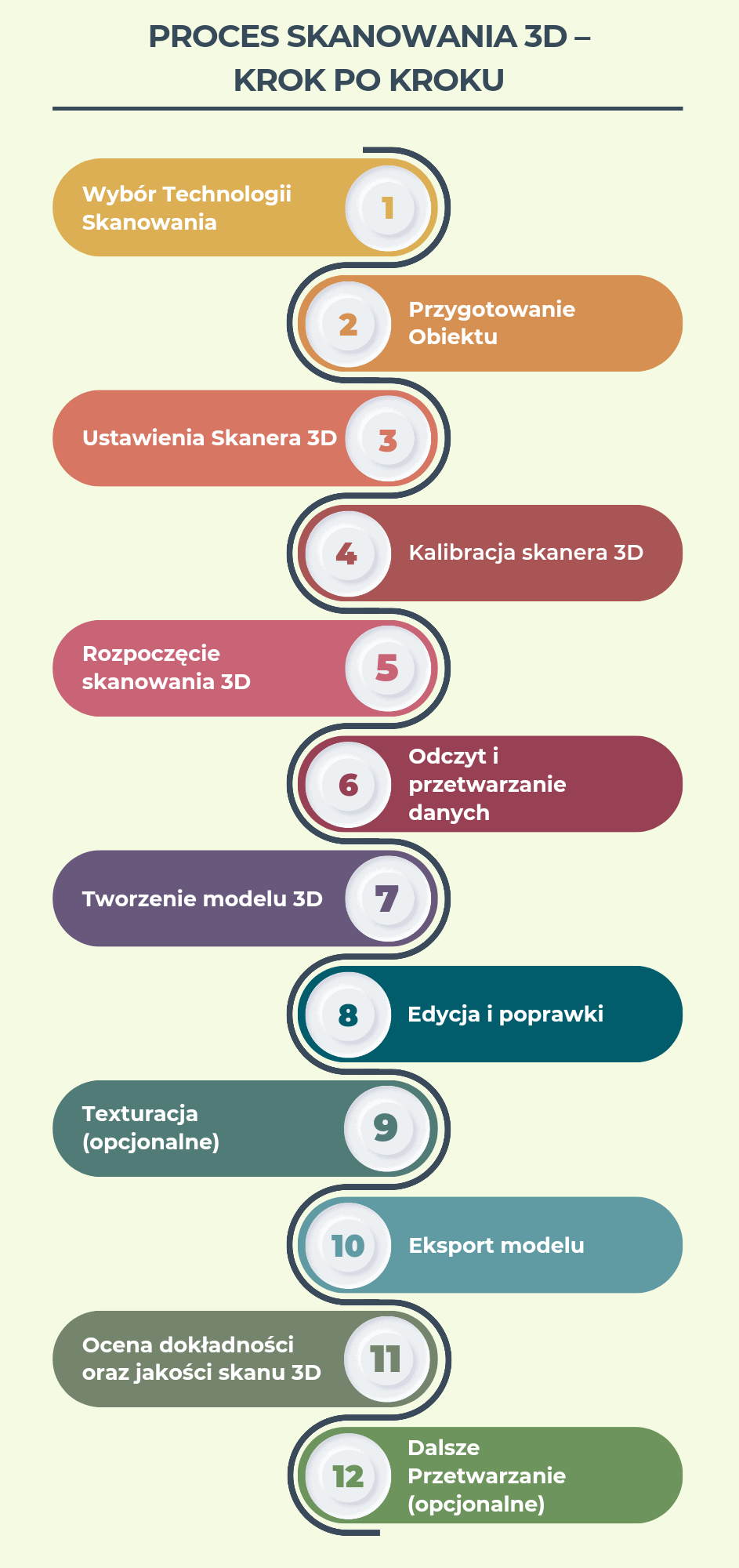
- Selecting Technology: laser, structured light, photogrammetry, or CT.
- Preparing the Object: cleaning, applying contrast spray, placing markers.
- Scanner Settings: selecting resolution and scanning parameters.
- Calibration: ensuring measurement accuracy.
- Scanning: collecting surface data.
- Data Processing: creating a point cloud.
- 3D Modeling: generating a model from the point cloud.
- Editing: removing errors, smoothing the mesh, making corrections.
- Texturization (optional): adding colors or textures.
- Export: saving to STL, OBJ, or other formats.
- Accuracy Assessment: comparing the model with the scanned object.
- Further Processing (optional): optimization, triangle reduction, compression.
Challenges and Future of 3D Scanning
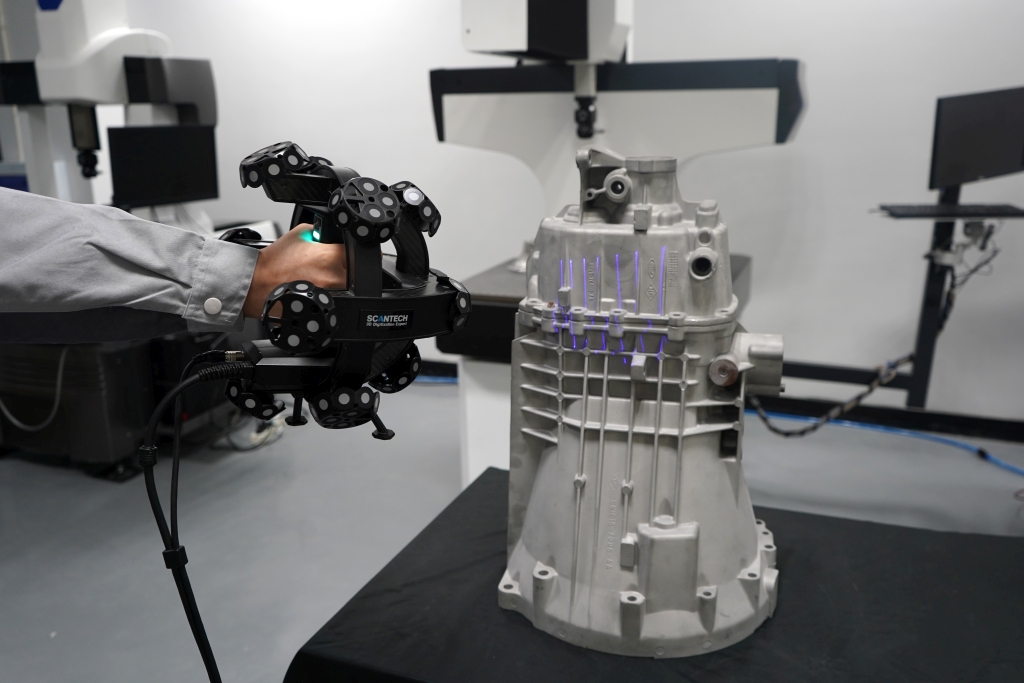
- New Technologies: AI, lidars, high-resolution sensors — higher precision, faster processing.
- Medicine: scanning for custom implants and prostheses — better fit and treatment effectiveness.
- Custom Production: integration with 3D printing allows flexible, cost-effective manufacturing of personalized products.
- Virtual Reality: using 3D scans in VR — design, training, exploration, architecture.
3D scanning is not just measurement technology — it is a tool that opens up the digital world of precise, realistic models. From industry to art, its development brings more and more possibilities for creating, analyzing, and recreating reality in virtual form.